HyperSound-Conditioner
Lubricant additive for all engine
and transmission oils
A technology product of the 21st century
What is the HyperSound-Conditioner
HyperSound Conditioner (HSC) is a lubricant additive for all engines and transmissions. HSC has a special inhibition (protective formula for soft metals).
By reducing friction losses by means of HSC you increase the efficiency of your combustion engine.
The result: fuel consumption drops significantly and you get up to 15% further with each tank of fuel for the same money.
- Up to 15% fuel savings
- sustainably reduces wear
- improves engine performance & running characteristics
- 100% free of solids
- Reduction of heat generation by up to 40%.
- improved running smoothness
- Reduction of the coefficient of friction by up to 80% already at start/cold start
- HSC is not subject to any special environmental protection restrictions.
- HSC is not harmful to health
- HSC is not toxic
- HSC is not toxic
- HSC is not a classic hazardous material & is also odorless
- extremely temperature-stable: stable pour point at - 42°C stable flash point at +122°C
- surface pressure test according to Reichert and Brugger - HSC reaches 235 N/mm2 (Brugger test DIN 51347/1+2)
- HSC viscosity: 17.9 mm2/s DIN 51562
Special features of our multiwave oscillator:
Application
Simply add HSC to the respective oil
Mixing ratio per 1L oil:
Engine 1:14 70ml
Gearbox 1:40 25ml
Hydraulics 1:64 16ml
Greases 1:5 200ml
Long lasting
The single HSC filling is sufficient for 20,000 km.
One product for all applications.
Advantages
Unlike conventional additives, HSC HyperSound Conditioner does not contain any solids (ceramics, PTFE, boron, graphite, etc.) Harmful deposition of solids in the engine, transmission or filter is therefore ruled out.
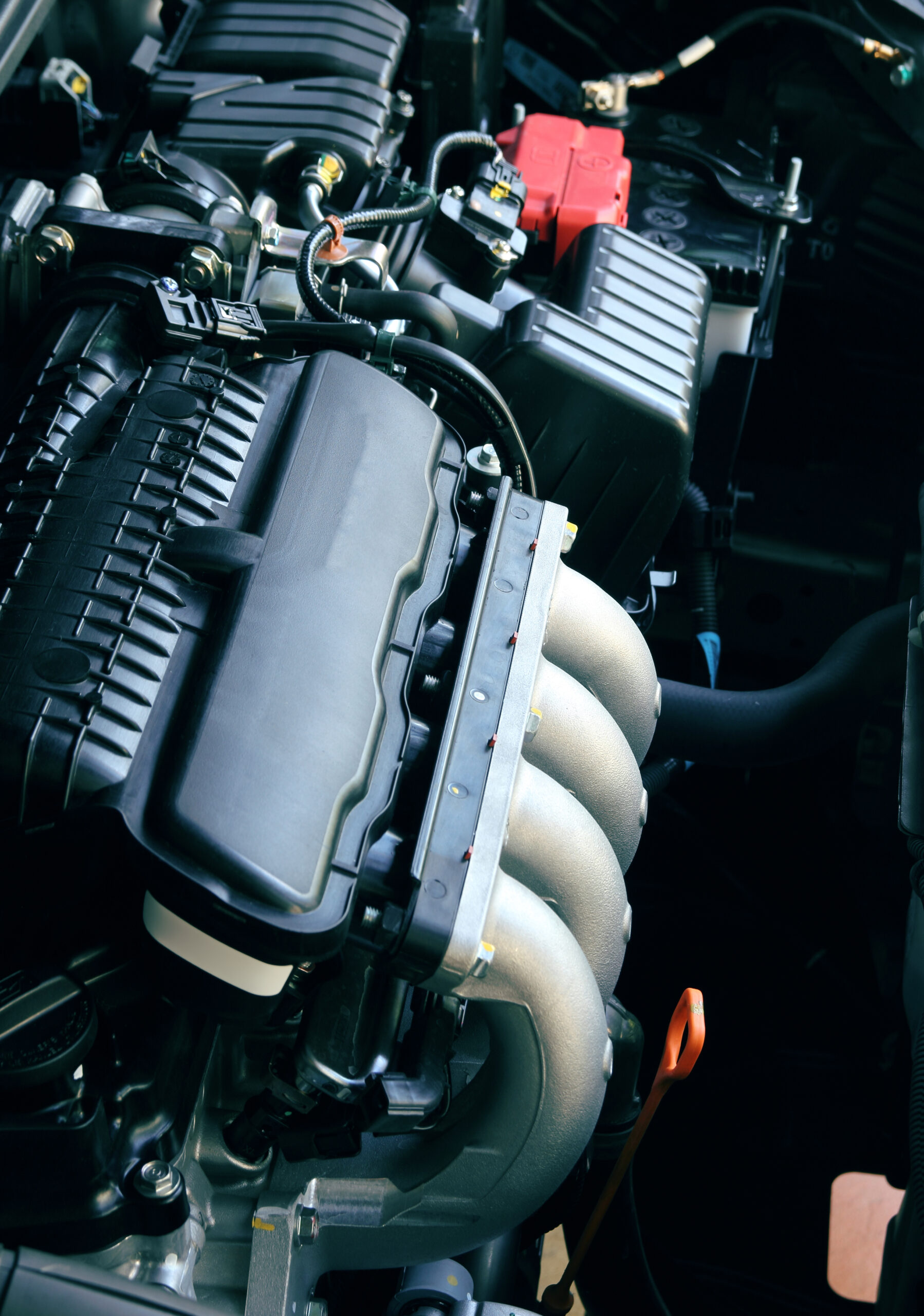
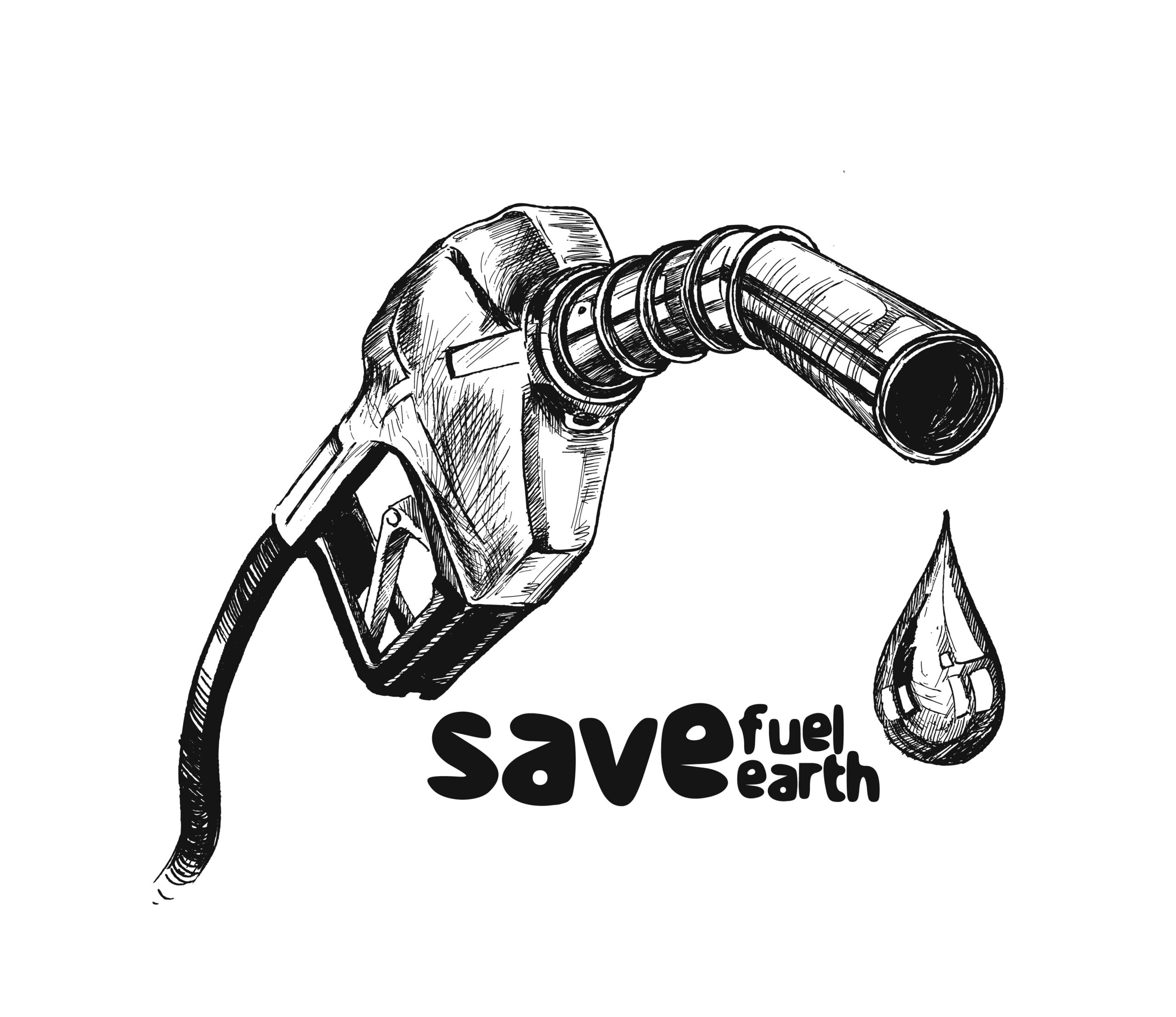
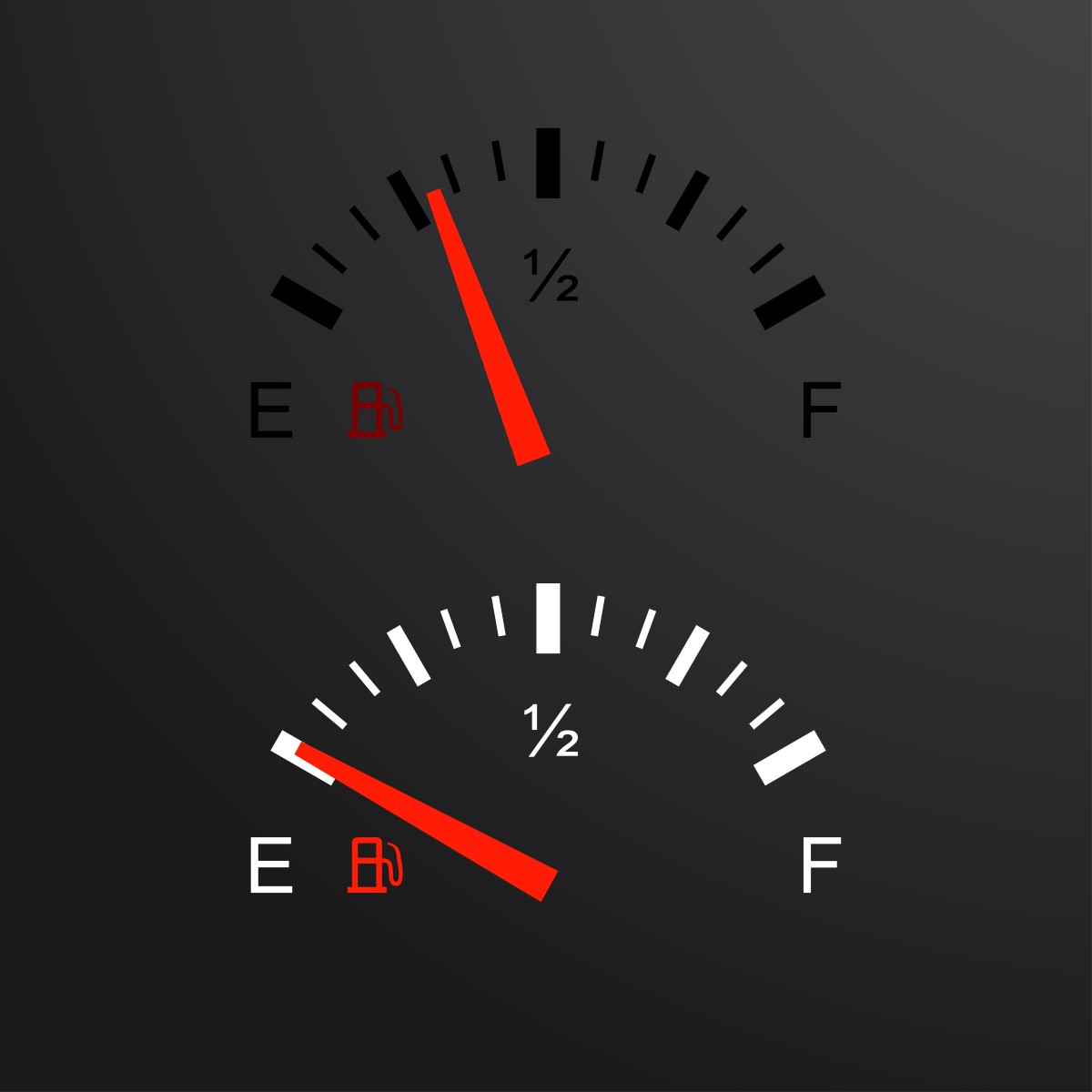
Application:
The quantity to be added depends on the required performance. The addition should always be pre-diluted to ensure rapid distribution.
The data and notes given here are to be regarded as guide values for normal cases. In all special cases, our technical service is available for advice.
4 stroke engines | Gearbox / Differentials | Automatic transmission | Hydraulic systems | Greases |
---|---|---|---|---|
1:14 to max 1:10 | 1:20 to max 1:10 | 1:30 to max 1:20 | 1:60 to max 1:50 | 1:5 |
≈ 70 ml to max. 100 ml | ≈ 50 ml to max. 100 ml | ≈ 30 ml to max. 50 ml | ≈ 16 ml to max. 20 ml | ≈ 200 ml |
7% bis max. 10% | 5% bis max. 10% | 3% bis max. 5% | 1,6 % bis max. 2% | ≈ 20% |
Support the Environment:
Thanks to HSC, you not only reduce your fuel costs, but also ease the burden on our environment.
C02 savings:
Gasoline engine Per 20,000 km: 839 kg C02
Diesel engine Per 20,000 km: 950 kg C02
Data basis: 15% fuel savings through HSC Consumption: 12 L per 100 km - Data: direct C02 emission.
WITH CERTIFIED OUALITY GUARANTEE according to DIN EN ISO 9001 and ISO 14001
Conserving resources, increasing energy efficiency
Environmental responsibility is the big issues of our time.
The "metal-metal friction" in the most diverse engines and aggregates, which cannot be overcome by the use of good lubricating oils alone, plays a very significant role worldwide. In fact, friction has always been viewed critically in the areas of mobility, production and energy generation, because it costs valuable resources, a high level of energy and, not least, large amounts of capital.
For decades, intensive research efforts have been made worldwide to solve this problem - but without being able to deliver sustainable or acceptable results - until now, because the new development of the HyperSound Conditioner sets fundamentally new standards.
TRIBOLOGY showed us THE WHAT, our scientists showed us THE HOW
and the numerous competitors showed us THE HOW BETTER NOT.
In TRIBOLOGY, the causes and effects of friction between two solid objects are researched with the aim of sustainably reducing the loss of energy and material that always occurs in this process.
Did you know, for example, that the surface of steel, even with the highest finishing quality, at electronic optical magnification of 1:10,000, resembles a wild mountain landscape (in technical terms: metallic roughness peaks)? And that two such metal surfaces, simply by close, resting contact, already enter into a high affinity relationship with each other, the so-called cold weld? And that here, due to the opposing working motion of the metal bodies, as in the case of an engine cold start, for example, abrasion-induced temperatures of over 1,000 C° occur, - because the "metallic roughness peaks" grind each other down? This is the cause of the well-known, worldwide high wear factor in engines, transmissions and aggregates of all kinds. - And this despite the use of the best lubricants or lubricant technologies!
Scientific studies in the field of friction theory show that the physically based frictional resistance, e.g. in drive units, consumes up to 25% of the generated energy unused in this way.
In everyday practice, however, a high coefficient of friction also manifests itself in strong heat generation and consistently high wear. The result is wear damage with sometimes disastrously far-reaching consequences. - In industrialized countries, one assumes an economic damage of 5% of the GDP (gross domestic product), which leads to an annual damage of 35 billion euros in Germany alone. - This is irrespective of the additional burden on the environment.
Conversely, this means that a sustainably reduced coefficient of friction always also leads to a reduction in heat and abrasion-related material wear, and consequently contributes to a significantly effective reduction in energy consumption as well as the wear-related damage rate and the resulting failure damage.
Testimonial:
Wir haben Ihr Produkt HSC HyperSound-Conditioner an einem Volvo FH 480 als Beimischung im Motorenöl getestet. Nach einer Laufleistung von 14.000 km haben wir eine Kraftstoffersparnis von 4,6 °/o festgestellt.
Desweiteren haben wir HSC HyperSound-Conditioner an weiteren Fahrzeugen im Einsatz.
Einzelne LKW's wurden komplett mit MTC bestückt, d.h. beim Motoren-, Getriebe-, Achs- und Hydrauliköl.
Wir sind über dieses Ergebnis sehr erfreut und können den Einsatz von HSC HyperSound-Conditioner auf jeden Fall weiterempfehlen.
TECHNICAL DATA
Product name: HyperSound-Conditioner
Additive for cutting and engine oils, not water soluble HyperSound-Conditioner is used wherever the performance of a cutting and forming oil is no longer sufficient. HyperSound-Conditioner improves the surface quality. Contains no flammable and health hazardous solvents.
Initial engine treatment Mixing ratio 1:14 (70ml/L oil) into the engine at operating temperature and continue (if possible in connection with an oil change) add to the engine.
This high-tech additive contains no suspended solid particles such as Teflon, ceramic or graphite. Unlike other oil additives, HyperSound Conditioner does not form coatings that can clog filters or form deposits on moving parts.
Instead, it creates a metal care system to reduce metallic friction.
HyperSound-Conditioner contains a special inhibitor that prevents attack on copper and copper-alloyed materials.
Characteristics:
Color: light
Density 15°C: 1,06 n. DIN 51757
Viscosity 40°C mm²/s: 17,9 n. DIN 51562, °E: 2,6
Flash point COC °C : 122 n. DIN ISO 2592
Specific surface pressure
according to Reichert N/cm²: 11.000
according to Brugger N/mm²: 235 n. DIN 51347/1+2
Pour point °C: -42n. DIN ISO 3016
Copper strip test 100 A 3: 1a n. DIN EN ISO 2160
Safety Data Sheet
Product name: HyperSound Conditioner
1. name of the substance, preparation and company
Product information:HyperSound-Conditioner
Recommended use: Additive
2. possible hazards of the preparation
Hazard description: N - Dangerous for the environment *
Information concerning particular hazards for human and environment:
R 50/53 - Very toxic to aquatic organisms, may cause long-term adverse effects in the aquatic environment*.
3. composition/information on ingredients
Chemical characterization:
Chlorinated kerosene
Hazardous ingredients:
EINECS-No. Designation Kennb. Content-% CAS-No. .............R-Phrases ......................................./.........................../
287-477-0 ......... Chlorinated kerosene (C14 - C17) ..........N..........................80
85535-85-9 .........(chlorine content 40 - 50%)* ............./.........................../
/.................. 50/53 * ........................................./.........................../
Composition/Information on ingredients
Additional information: Quality contains chlorine, contains no zinc and no barium.
4. first aid measures
General advice: Medical attention is required in all cases of ingestion, inhalation, eye contact and skin contact.
After inhalation: Remove persons to fresh air.
After skin contact: In case of contact with skin, rinse preferably with plenty of pure water and clean with soap. Treat contact site with suitable skin protection and skin care products.
After eye contact: In case of eye contact, rinse eyes with water for sufficient time (15 minutes) with eyelids open.
After ingestion: Rinse mouth with lukewarm water, do not induce vomiting! The affected person can drink 2-3 cups of water or milk.
Get medical help.
5. fire fighting measures
Suitable extinguishing media: water spray, foam, sand, carbon dioxide, extinguishing powder.
Unsuitable extinguishing media for safety reasons: Full water jet
Special hazards caused by the substance or preparation itself, its products of combustion or resulting gases: Product decomposes at elevated temperatures, producing hydrogen chloride. Limit hazardous area, weather conditions - observe wind direction and speed (main condition).
Special protective equipment for fire fighting:
Do not inhale explosion and fire gases, to wear self-contained breathing apparatus (isolator).
Additional advice: Cool endangered containers with water spray.
6. measures in case of accidental release
Personal precautions:
Protective clothing, gloves and footwear, tight-fitting safety glasses or face shield, respiratory protection.
Environmental precautions: Prevent dispersal. Do not allow to reach ground water and surface water. Dispose of spillage in accordance with regulations. Cover residues of this product with non-combustible, liquid-binding material e.g. sand, perlite, collect in waste containers and dispose of.
Methods for cleaning up/taking up:
Dispose of residues and contaminated absorbent materials in special facilities designed for incineration of chlorinated hydrocarbons.
7. handling and storage, advice for safe handling
Prevent spreading. Do not allow to enter ecosystems.
Advice on protection against fire and explosion: No special measures required.
Storage, requirements for storage rooms and containers:
Store chlorinated kerosenes in dry areas protected from weather conditions. Keep containers tightly closed.
Information on storage in one common storage facility: Do not store together with foodstuffs.
Further information on storage conditions: Recommended storage temperature 20 °C, protect from frost and heat. Always keep container closed.
8. exposure controls, personal protection equipment
Additional information on the design of technical equipment: see 7
Components with limit values that require monitoring at the workplace: *Designation: Oil mist
Type: TWA
Value: 5
Inh.: mg/m³ *
Additional information: None *
Respiratory protection: Gas/vapor filter
9. hand protection: liquid-tight protective gloves
Eye protection: Tightly fitting safety goggles and face shield
Body Protection: Wear appropriate work suit and safety shoes, do not wear jewelry.
Protective and hygienic measures:
Avoid contact with eyes and skin. Observe general rules of industrial safety and hygiene.
Physical and chemical properties, appearance
Form: liquid - Color: light - Odor: characteristic
Safety relevant data
Value Unit Method
Density: .............................at 15 °C ........1.06 ..............g/cm³ ................ DIN 51757
Viscosity: ........................at 40 °C .......17,9 ..............mm²/s ............... DIN 51562
Lower Ex-limit: ............n.a. ................. Vol.% ............/ ......................... /
Upper Ex-limit:w ..........n.a. ................. Vol.% ............/ ......................... /
Solubility in water: .....insoluble .......... /...................../ ......................... /
Flash point: ....................122 ................. °C ................../ ......................... DIN ISO 2592
Ignition temperature: ..............200 ................. °C ................../ ......................... /
11. stability and reactivity
Conditions to avoid: At elevated temperatures, the product decomposes, producing hydrogen chloride.
Materials to avoid: acids, oxidizing agents, alkali and alkaline earth metals which have a strong affinity for chlorine.
Hazardous decomposition products: Hydrogen chloride
12. toxicological information
Field Experience/Other Observations:
There is no information that the product or its components may be respiratory sensitizing and/or skin sensitizing.
General remarks: Not likely to cause cancer under normal use and observance of usual precautions.
Other comments: Chlorinated kerosenes have very low toxicity to humans.
Observations Relevant to Classification: The highest concentration at which no adverse effects were noted in rats (NOEC) is 10 mg/kg/day. This value is higher than the highest exposure achieved in industry, under normal conditions. Several studies have been conducted that were adjusted for the carcinogenic effects of chlorinated kerosenes. In the few studies, occurrence of tumors has been noted only in rats and mice.
13. environmental information
Product is poorly biodegradable. Degradation rate is 1.9-7.2 days. Do not allow uncontrolled release of product into the environment.
14. notes on disposal
Product Recommendation: Dispose of residues and contaminated absorbent materials in special facilities designed for incineration of chlorinated hydrocarbons.
Waste code and designation: 120106 halogenated mineral oil based machining oils (except emulsions and solutions).
Uncleaned packaging Recommendation:
Contaminated packaging should be emptied in the best possible way, it can then be reused after appropriate cleaning.
15. transport information
Land transport: ADR/RID Class: 9, Hazard label: 9, UN number: 3082
Description of goods: ENVIRONMENTALLY HAZARDOUS SUBSTANCE, LIQUID, N.O.S.
Contains: Chlorinated kerosene C14 - C17, Packing group: III
Sea Transport: IMDG Class: 9, EmS No.: F-A, S-F, UN No.: 3082
Proper shipping name: Environmentally hazardous substance, liquid, n.o.s.
Contains: chlorinated hydrocarbons C14 - C17, Packing group: III
Marine pollutant: no
Air transport: IATA class: 9, UN number: 3082
Proper shipping name:Environmentally hazardous substance, liquid, n.o.s.
Contains:chlorinated hydrocarbons C14 - C17, Packing group: III
Purchase HyperSound-Conditioner
HyperSound-Conditioner:
€
200,-
+ VAT + shipping
Yearly
$
890.99
/ year
Extra premium features and instant access to amazing case studies
Note on the following test results
The Vibration Friction Wear Tester (SRV®) was developed to investigate the friction wear that occurs as a result of vibrations with very small amplitude and high frequency. A stationary steel ball is oscillated against a stationary steel cylinder on the end face.
Lubricating oils, greases, pastes, dispersions and dry lubricating films can be run at various loads until the lubricating film breaks down. The purpose is to determine the effect, load capacity and service life of lubricants and their additives under oscillating movements. In general, it should be noted that the oscillating load is significantly "sharper" than a purely rotational movement, since the zero point of velocity is repeatedly traversed and thus boundary or mixed friction occurs again and again.
The lubricants were tested in accordance with DIN 51834 Part 2. Under these test conditions, two test runs were carried out in each case with a fully synthetic branded high-performance engine oil 0W-40 and then with this oil mixed with 7% HyperSound conditioner.
Significant improvements were achieved after adding the conditioner, resulting in a significant reduction in wear and a significant reduction in the friction coefficient level. When components move against each other, friction is generated. This energy, lost in the form of heat, is directly reflected in consumption. The more frictionless a unit runs, the less energy is consumed and therefore the lower the operating costs. In addition, special lubricants often have a direct influence on the quantities of lubricant consumed as well as on the maintenance intervals and service life of lubricated components.
The test methods according to the relevant standards are used to determine characteristic values for lubricants with active ingredients that are intended to reduce wear between surfaces moving relative to one another. The results explicitly refer to the respective test setup.
The Brugger test (DIN-51347) and the test with the Reichert friction-wear balance operate in the range of mixed friction. Both tests are used to determine characteristic values for lubricants with regard to their behavior under sliding stress under these conditions.
The test results describe the behavior of the lubricants in a tribological system in which mixed friction occurs between steel friction partners.
Several test runs (at least 3) were carried out using each test method with a fully synthetic branded 0W-40 high-performance engine oil and then with this oil mixed with 7% HyperSound conditioner.
Significant improvements were achieved in each test after adding the conditioner.
In both the Reichert and Brugger tests, the added conditioner resulted in significant wear reduction. Likewise, a significant improvement in pressure absorption capacity (EP behavior) was achieved in these tests.
The test methods according to the relevant standards are used to determine characteristic values for lubricants with active ingredients that are intended to reduce wear between surfaces moving relative to one another. The results refer explicitly to the respective test setup.
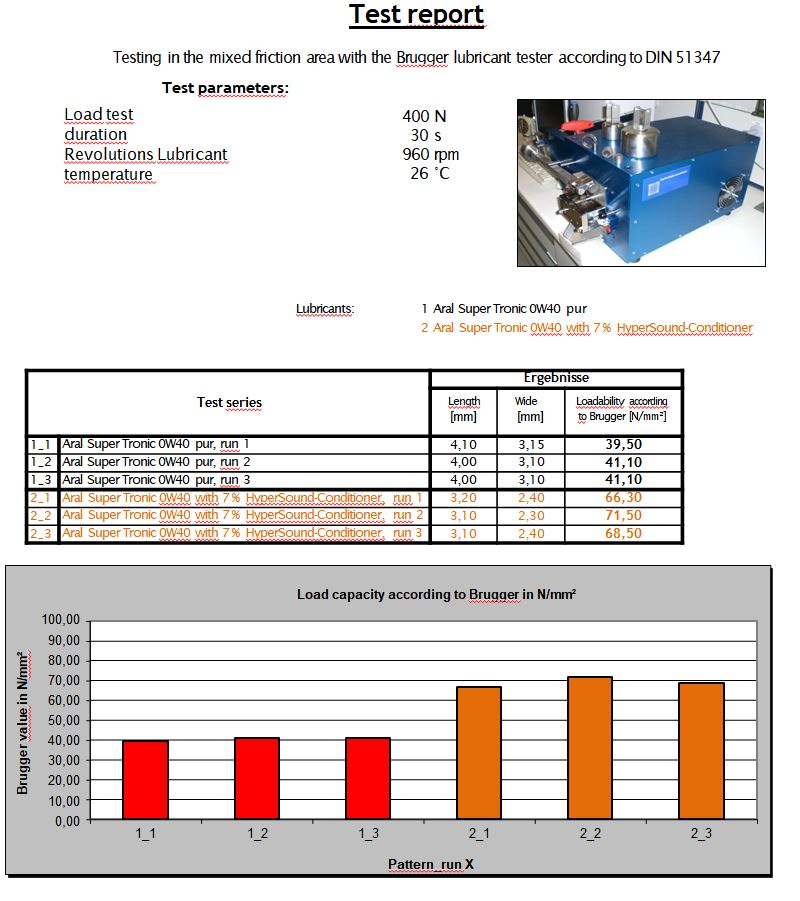